Why Food Manufacturers are Moving to the
HDX 250A Combo Shrink Wrapping System
Compact, fully electric shrink wrapping system with built-in sealer and tunnelโcutting costs, saving space, and eliminating compressed air.
In the food manufacturing industry, shrink wrapping is a widely used packaging methodโtrusted for extending shelf life, providing tamper-resistant protection, reducing food waste, and enhancing visual appeal with the option of printed shrink film.
To achieve this in the smartest and most cost-effective way possible we step in with the Automatic Combo Shrink System HDX-250A. An all-in-one unit combining a high-speed L-bar sealer with a built-in shrink tunnelโ built to eliminate the need for separate machines and slashing equipment costs by up to 40%.
This combo machine is fully electric with zero air requirements and offers plug-and-play convenience, fast tool-free changeovers, and intuitive touchscreen controls. With speeds up to 35 packs per minute, it’s engineered for high-throughput production without sacrificing quality or floor space.
COMPACT FOOTPRINT
Combines an automatic L-Bar sealer and shrink tunnel into one unit.
FULLY ELECTRIC
100% electric for easy installation and hassle-free operation.
HIGH-SPEED OUTPUT
Achieve up to 35 packs per minute with minimal operator input.
COST SAVINGS
Up to 40% Cost Savings โ eliminates need to purchase separate equipment.
Why choose the Automatic Combo Shrink System HDX-250A?
A space-saving, food-industry workhorse designed for fast, clean, and efficient shrink wrapping.
Shrink wrapping plays a huge role in the frozen food industry as it is integral in securing products in a way that maintains freshness and security. This is done by protecting the product during transit and serves as a barrier against moisture and freezer burn โ extending the product’s shelf life. The shrink film combines with heat, and seals around the product, fully enclosing it.ย
The HDX-250A Automatic Combo Shrink Wrapper is specifically built to excel in these high-demand settings. Its all-in-one, fully electric design combines an automatic L-Bar sealer and built-in shrink tunnel into one compact, efficient system. This makes it faster, cleaner, and simpler to operate than traditional two-machine setupsโwhile still delivering tight, consistent wraps on a wide range of frozen formats.
Most importantly, the HDX-250A delivers the level of seal integrity and package durability that frozen foods require. ย With features like precise film control, automatic feeding, and high-speed operation the HDX-250A keeps your line running smoothly and your products looking flawlessโright from the freezer to the shelf.
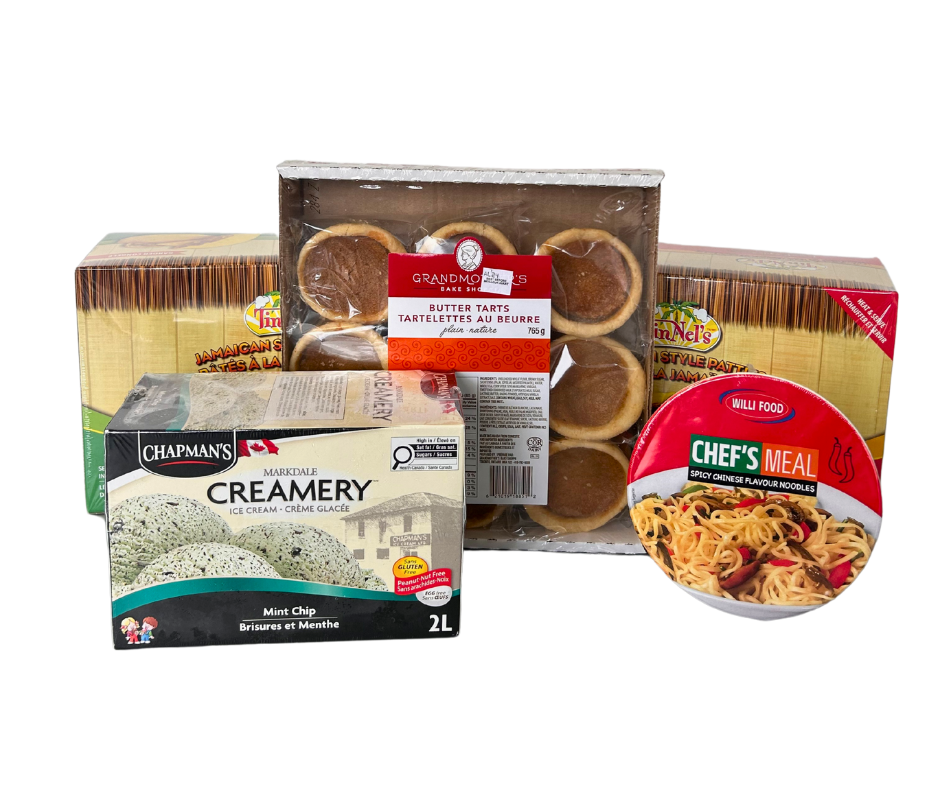
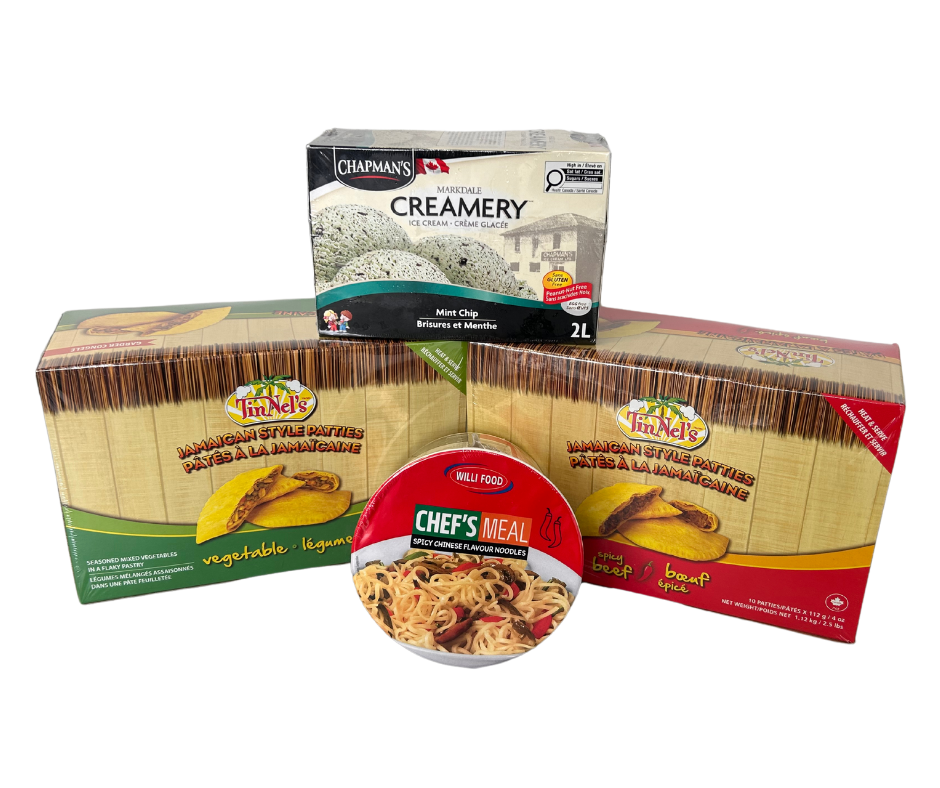
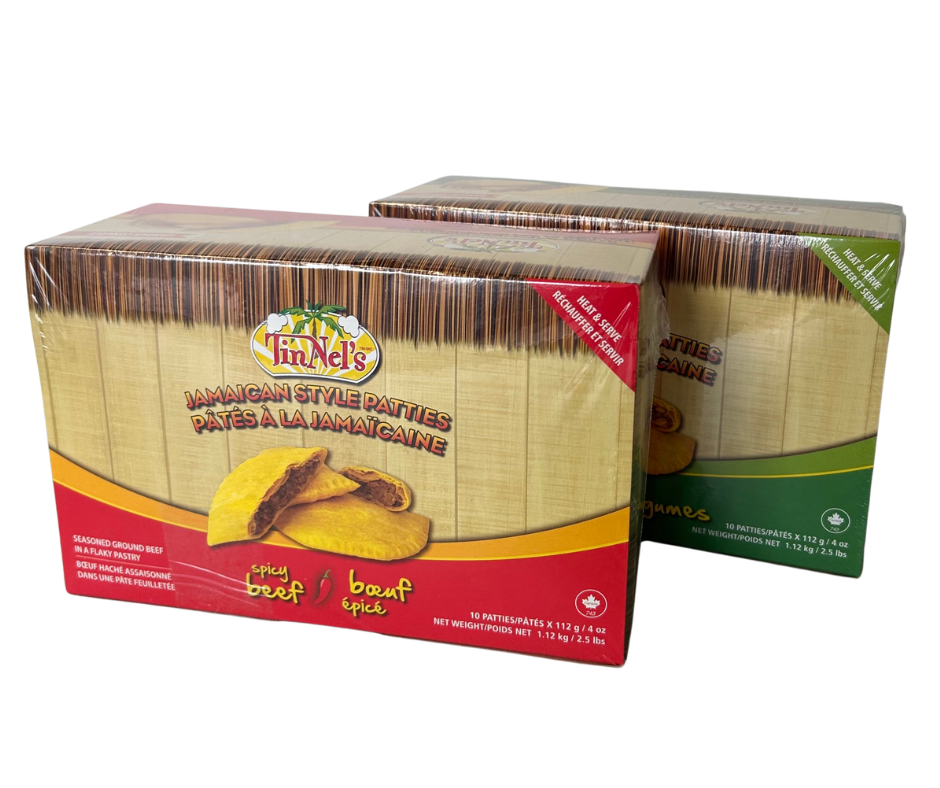
Maximize ROI with the HDX-250A
The HDX-250A replaces two machines with one compact, fully electric systemโcutting floor space, energy use, and maintenance costs – maximizing your return on investment!
Impak Packaging leads the industry in ROI-focused solutions. We help manufacturers lower packaging costs, boost efficiency, and get faster payback with expert support and flexible purchase options.ย
BUYING
Avoid long lead times and get your fully electric, all-in-one shrink system delivered fast. Perfect for food manufacturers who need a turnkey solution without delays.
FINANCING
Upgrade your packaging line without the upfront investment. Flexible financing plans are available to match your budget and cash flowโwith full ownership at the end of the term.
RENTALS
Rent the HDX-250A on a monthly or yearly basisโideal for managing seasonal demand, capacity surges, or pilot programs before committing to a purchase.
BUYBACK
Using older shrink equipment? Weโll buy it back and apply the value toward your new HDX-250Aโhelping you modernize while minimizing waste and upfront cost.
Shrink Smarter: Unlock Better Results with Cryovacยฎ Shrink Wrapping Materials
As the exclusive distributor of Cryovacยฎ shrink film, Impak delivers high-performance materials perfectly matched to the HDX-250A. From trays and cartons to retail-ready packs, our film is engineered for optimal resultsโbacked by expert support tailored to your product and equipment.
Looking for a Shrink Wrapping System?
Just give us a call orย send us a messageย with the form below. One of our customer service representatives would be happy to help you with whatever you need.
400 Flint Rd.
North York, Ontario
M3J 2J4
Phone:ย 416-299-0960
Fax: 416-299-0961
Email: [email protected]